INSULIN PUMP CONTROLLER DEVELOPMENT FOR AN AUTOMATED INSULIN DELIVERY SYSTEM
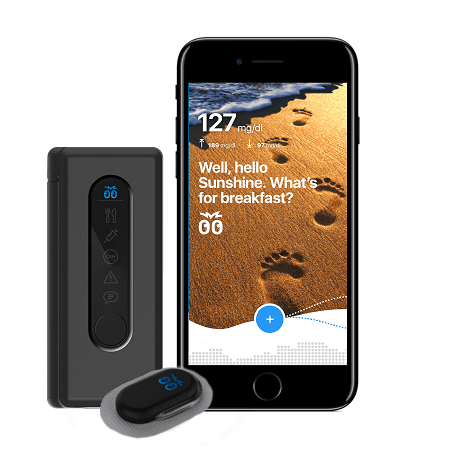
Bigfoot Biomedical, a high-profile startup on a mission to improve the lives of Type 1 diabetics (T1D), selected NOVO to develop the insulin pump controller for their automated insulin delivery system. After observing family members struggle to manage the disease, one of Bigfoot’s founders, Bryan Mazlish, recognized the need for a system that would reduce the cognitive burden on diabetic patients and their caregivers—an automated system to perform glucose measurement and automate the medication administration. He also recognized that the individual elements needed to implement such a system already existed. To demonstrate the concept, Mazlish integrated an existing blood glucose meter (BGM), continuous glucose monitor (CGM), diabetes therapy pump, and smartphone into an automated system that closed the loop around blood glucose using a dose-delivery algorithm he developed. Reactions from T1D patients strongly endorsed the concept, and Bigfoot Biomedical was born.
Bigfoot began to assemble a commercialization team, and on the advice of several of their industry contacts, selected NOVO as their engineering partner. NOVO made recommendations for industrial design and human factors consultants, while Bigfoot recruited several key medical device development experts to create the core development team.
COMPONENTS OF THE INSULIN DELIVERY SYSTEM AND NOVO’S ROLE
The development team pooled their industry knowledge and the details of the commercial version began to emerge. The connected health system would include an existing BGM, The Abbott FreeStyle Libre 2 CGM, a mobile medical application, web services, an existing FDA-approved insulin pump, a new pump controller, and a mobile device (smartphone). There was an obvious risk of complexity if the system integration was not executed well, and the team committed itself to creating software for the insulin pump controller and smartphone that would provide a seamless experience for the user.
NOVO’s role in the project was to develop the electronics hardware and embedded software for the proprietary insulin pump controller, as well as the enclosure and external interfaces between the pump controller and the pump body for this Class III medical device. NOVO also assembled the first run of clinical trial units under our ISO 13485;2016 certification.
THE TECHNICAL AND DESIGN CHALLENGES: POWER MANAGEMENT, INGRESS PROTECTION, SAFETY, AND RELIABILITY
Some of the technical challenges NOVO had to overcome on this project included:
- Designing for ingress protection rating of IPX8 for the durable insulin pump controller when connected to the pump body.
- Power management for the custom electronics that had to support power-intensive functions such as the pump drive and the Bluetooth Low Energy (BLE) wireless interface between the system components while meeting the safety and reliability requirements of a Class III device.
- Maintaining security of data transmissions between system components for HIPAA compliance and to harden the system against intrusions (hacking).
- Implementation of the user interface and industrial design solutions provided by other design partners while maintaining functional requirements.
THE ENGINEERING BEHIND GREAT PRODUCTS
NOVO provided the medical device electronics, embedded software (firmware), mechanical engineering for the enclosure, and pre-production manufacturing for clinical trial units in well under one year. Each of the technical challenges mentioned above required innovative design and verification testing to overcome.
- The enclosure design and the mechanical and electrical interfaces between the pump controller and the pump body required an innovative sealing design.
- A modular electronics architecture was developed that separates key functions to minimize power consumption, maximize reliability, and maximize maintainability. BLE parameters were optimized and the antenna was tuned to ensure reliability of communications.
- With power management solutions implemented, the pump controller can still communicate with the mobile medical application at range of approximately 25 feet.
- Fail-safe designs for critical electrical failure modes were implemented to ensure patient safety. This includes multiple annunciators on the controller for audible, visual, and tactile feedback, in addition to the annunciators on the mobile device, all employed by the system to notify the patient of alarm and alert conditions.
- The electronic hardware design was miniaturized to minimize the overall volume of the pump controller/pump body assembly.
- In addition to design and development, NOVO provided manufacturing services for Bigfoot’s first clinical trial units. Several hundred units were assembled under the pilot manufacturing procedures contained in our ISO 13485: 2016-certified quality system. The controlled build included manual and automated assembly and QC fixtures, material traceability, device master record (DMR) documentation, work instructions, and lot history records. All the manufacturing documentation was transferred to Bigfoot for use in their regulatory filings, as well as for use in their own manufacturing facility.
The fast pace, technical challenges, and regulatory path for this product made NOVO one of the few viable engineering partners. Our expertise in electromechanical medical devices, specifically, drug delivery devices, as well as in medical embedded software development, made NOVO the right choice for Bigfoot. We are proud to be a part of what will be one of the first automated insulin delivery systems on the market.
Learn about our firmware development for this product here.
Watch a video about the Bigfoot Biomedical product.