Overview
Minimally invasive treatments for weight loss are increasingly favored in today’s healthcare market, especially solutions that avoid surgery and offer an improved patient experience. Years ahead of this trend, Obalon Therapeutics partnered with NOVO to develop a swallowable intragastric balloon system. The result was a visionary device combining mechanical precision, biocompatible materials, and early electronic controls to support effective, non-surgical weight loss.
Obalon sought NOVO’s expertise to help design the balloon, develop the inflation system, create the delivery mechanism, and establish manufacturing processes for the complex technical films involved. NOVO’s role expanded to include developing mechanical and electronic pressure regulation systems, embedded software, and a graphical user interface to optimize both clinical ease-of-use and patient safety.
Key Engineering Challenges & Solutions
Challenge | NOVO’s Solution |
---|---|
Balloon deployment in harsh gastric environment | Developed robust seam designs, heat-sealing processes, and folding methods using chemically resistant, laminated films to withstand stomach acid and mechanical abrasion. |
Controlled inflation after ingestion | Designed a precise mechanical back-pressure regulator and an advanced electronic pressure regulation system with altitude compensation. |
Inflation tube separation post-deployment | Engineered a reliable mechanical disconnect system between the inflation tube and the implanted balloon. |
Smooth geometry for patient safety | Developed thermoforming techniques and proprietary joint designs to create a smooth balloon surface, minimizing irritation risks. |
Manufacturing scalability | Created proprietary manufacturing and testing methods to support clinical trial builds and future production needs. |
Technical Innovations & System Design
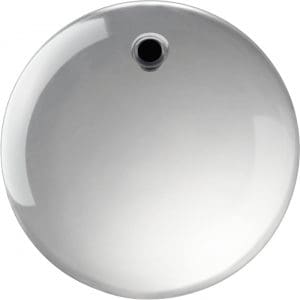
Mechanical & Electrical Design
- Inflation Control: Designed both a mechanical regulator for precise pressure control and an electronic regulation system capable of adjusting for ambient pressure variations.
- Balloon Material Engineering: Advanced multilayer film processing to ensure chemical resistance, durability, and minimal seam stress under stomach conditions.
- Miniature Valve Integration: Developed a compact valve assembly enabling inflation and automatic disconnection post-procedure.
Software & Controls Development
- Graphical User Interface: Created an intuitive GUI with animated, step-by-step physician instructions to guide the inflation process, improving procedural reliability.
- Power Management: Optimized embedded system design for battery operation, addressing critical runtime and reliability requirements for portable medical devices.
Process Engineering
- Manufacturing Process Development: Innovated folding and sealing methods to consistently encapsulate the balloon in a small, swallowable gel capsule.
Human Factors & Usability
- Focused on minimizing physician training time and maximizing patient safety by integrating user-friendly controls, visual guidance, and robust fail-safes into the system.
Results & Impact
Clinical Success: The system demonstrated significant weight loss outcomes with no serious adverse events in clinical trials.
Regulatory Achievement: Obtained FDA Premarket Approval (PMA) in record time for its device class.
Commercial Milestone: Obalon Therapeutics’ innovative intragastric balloon technology contributed to its merger with ReShape Lifesciences (RSLS), enhancing the combined company’s portfolio of non-surgical weight loss solutions.
Intellectual Property: NOVO’s contributions resulted in multiple issued U.S. patents (8 647 358; 8 740 927; 9 173 758; 9 351 862).
Why NOVO Engineering?
Today’s obesity treatment landscape increasingly embraces minimally invasive, patient-centered solutions — combining mechanical, electronic, and software innovations. NOVO’s work with Obalon was an early example of this shift, integrating precision engineering, smart controls, and human-centered design long before these were standard market expectations.
Our ability to foresee where the industry was heading, toward safer, simpler, tech-enabled treatments, positioned our client for regulatory and commercial success. This project exemplifies NOVO’s strength in bringing visionary medical technologies to life.
Ready to Transform Your Medical Device Vision?
Contact NOVO today to discuss how we can help solve your engineering challenges and deliver next-generation solutions.