Client Need & Project Overview
A biotechnology company specializing in bio-based chemical manufacturing needed to automate its long-term cell culture experiments. These experiments involved growing cultures over many generations to study evolutionary outcomes in controlled environments. NOVO was engaged to develop a quasi-continuous system, internally referred to as Automated Evolution, that would automate environmental control, cell density monitoring, media exchange, and growth cycle transitions with minimal human interaction.
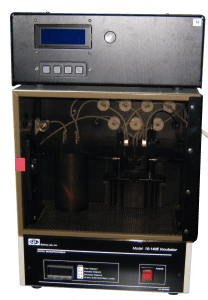
Key Engineering Challenges & Solutions
Challenge | NOVO’s Solution |
---|---|
Measuring cell density in a flow field | Developed a custom cell density meter based on opacity. Cell density was the process variable used to trigger automated growth cycles. |
Ensuring uniform mixing in an anaerobic environment | Designed a system using humidified, pressurized gas and pinch valves to ensure uniform mixing of the cell culture. |
Maintaining sample sterility | Non-contact ultrasonic level sensors were incorporated into the level control algorithm. |
Controlling temperature and levels during growth | Developed custom firmware to control the process, enable the user interface, and manage error conditions. |
This automated approach allowed the device to monitor cell density in real time and perform growth cycle resets automatically, removing part of the culture and introducing fresh growth media, thereby supporting multi-generational evolution studies.
Technical Innovations & System Design
- Mechanical & Electrical Design: Implemented a system of pressurized, humidified gas and pinch valves for efficient mixing in a sterile, anaerobic environment. These components were selected for performance and ease of sterilization between experiments. Tubing sets and wetted materials were designed for autoclaving and quick replacement.
- Software & Controls Development: Developed custom firmware and PC software, enabling a single PC to manage up to five units with individualized settings.
- Process Engineering: Proprietary cell density measurement and mixing solution; sterility control & maintenance; temperature control; and control algorithm.
- Human Factors & Usability: Engineered minimal user interaction, allowing automated operation for up to a month at a time. The system’s ability to autonomously manage feed cycles and maintain optimal conditions over extended timeframes enabled researchers to observe cell behavior over multiple generations.
Results & Impact
- Improved Efficiency: Reduced manual intervention, enabling long-term automated operation. The quasi-continuous system eliminated the need for researchers to monitor and manually intervene in cell culture experiments, making it possible to conduct complex biological studies with minimal technician intervention.
- Reduced Tech Labor: A total of nine systems were delivered, which were immediately incorporated into our client’s drug discovery and development process.
- Performance: The system met all performance and reliability requirements, exceeding client expectations.
- Cost-Effective Development: Time and budget estimates were within 10% of original estimates.
Why NOVO Engineering?
The custom system developed by NOVO tackled many of the same challenges that modern cell culture platforms address today. Features like closed sterile fluid handling, non-contact sensing, and long-duration unattended operation are now common across commercial systems; however, NOVO built this solution years ahead of market trends. By combining mechanical precision with smart controls and minimal user input, the system demonstrated how thoughtful design leads to increased efficiency and reliability.
Since then, the field has expanded significantly. Off-the-shelf platforms now offer parallel bioreactor control, single-use components, and integrated analytics to support high-throughput experiments and scalable production. Despite these advances, the core requirements remain the same: sterility, consistency, and ease of use. NOVO’s early approach to automation continues to align with where the industry is headed, underscoring the lasting value of custom solutions built around real-world user needs.
Connect with us about your automation projects!
Are you facing complex automation or instrument development challenges in your medical device or biotechnology applications? Contact NOVO Engineering to discuss how we can develop a tailored solution to meet your needs.