Translating a Vision for Agricultural Innovation into a Rugged, High-Throughput Engineering Solution
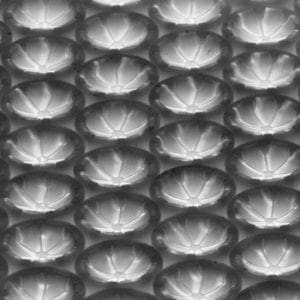
Client Need & Project Overview
Syngenta, a global leader in agricultural science, partnered with Diversa Corporation (now part of Verenium) to develop a next-generation leaf sampling platform to support marker-assisted selection (MAS). MAS enables the rapid identification of desirable plant traits using genetic markers without introducing foreign DNA – a technique that has become foundational to non-GMO crop development.
While the biological requirements and use case were clearly defined by Syngenta and its collaborators, they needed an engineering partner to translate this vision into a scalable, user-friendly system that could operate reliably in the field. NOVO was selected to design and develop the complete electromechanical and embedded software system for this initiative.
Key Engineering Challenges & Solutions
Challenge | Engineering Solution |
---|---|
Harsh field conditions including exposure to dust, dirt, and moisture | Ruggedized housing, sealed interfaces, and shock-mounted internal components |
Handling sticky, fibrous leaf tissue | Custom punch mechanism with internal lubrication and dislodging features |
Ensuring clean, traceable sample collection | Barcoded sample cassettes with individual containment wells and indexing system |
Minimizing user burden and training requirements | Intuitive UI with error detection and recovery features |
System integration with Syngenta’s lab software and sample workflows | Embedded PC with configurable barcode schema and LIMS integration |
Cost-effective manufacturing at scale | Injection-moldable cassette parts designed for automated assembly and reuse |
Technical Innovations & System Design
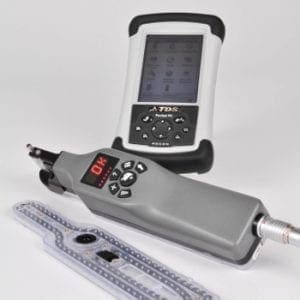
Mechanical & Electrical Design:
The handheld field device featured a proprietary cassette containing a track of indexed sample containers. The device managed cassette rotation, barcode scanning, and a punch system capable of sampling sticky plant material. A wearable system hub provided power, fluid, and computing resources via a ruggedized hybrid cable.
Software & Controls Development:
Technicians used the system to scan plant and cassette barcodes, enabling real-time sample traceability and error reporting. A compact embedded PC interfaced with Syngenta’s LIMS software to configure sampling protocols in the field.
Process Engineering:
In addition to the sample collection hardware, NOVO supported the development of lab automation tools to reformat samples from proprietary cassettes into standard microplates, and systems to clean and reuse cassettes.
Human Factors & Usability:
Designed for field use by technicians of varying skill levels, the system emphasized fast setup, minimal training, and recovery from interruptions—all while maintaining sample integrity and traceability.
Results & Impact
- Increased sampling throughput and consistency across multiple environments.
- Maintained sample integrity and barcode-based traceability throughout the workflow.
- Enabled scalable support for marker-assisted selection programs.
- Secured multiple U.S. utility patents (8 758 638 and 7 980 148).
- Successfully deployed in Syngenta’s operational workflows.
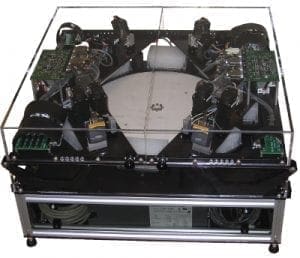
Why NOVO?
Syngenta’s development partners brought forward a clear concept: a more scalable and precise method of collecting plant samples to support their molecular breeding programs. NOVO served as the conduit between that vision and a fully engineered solution, delivering the hardware, software, and system architecture to make the product a reality.
This collaborative effort resulted in a rugged and reliable platform that enabled MAS – a approach that helped pave the way for today’s non-GMO innovation strategies. Modern companies like Cibus continue to build on this legacy, applying gene editing to achieve non-GMO crop improvements that rely on the same principles of traceability, sample fidelity, and scalable biology workflows.
NOVO’s role was not in defining these scientific goals, but in building the tools to help experts realize them. Our engineering work – grounded in precision, usability, and integration – remains a key enabler for life science innovators.
Connect with us about your automation projects!
Are you facing complex automation or instrument development challenges in agriculture, biotechnology, or life sciences? Contact NOVO to explore how our engineering expertise can help transform your vision into a reliable, real-world solution.