Optomechanical Engineering: Sensor Development
A machine vision company selected NOVO to provide the optomechanical engineering for their next-generation, 3D laser displacement sensor. In this product, a model of the three-dimensional surface is generated by translating an object beneath the sensor. The surface data can then be processed with existing machine vision software.
Hardware Design
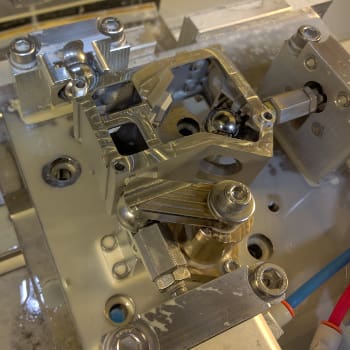
The laser source, optics, and CMOS image sensor had to be precisely aligned and held in a rigid, thermally stable housing. A rigid chassis was designed that allowed convenient secondary machining operations to establish datum features for the optics. The laser source and the image sensor were aligned dynamically using a vision-guided robot. Components were then bonded in place using a specialized adhesive system. Kinematic mounting methods were used to assure components were not over constrained after cure. Sensitive components were thermally connected to the cast-aluminum chassis, which acted as a heat sink.
A proprietary method was developed in NOVO’s internal machine shop to fabricate the luminescent targets used for sensor training and alignment. Custom laser-machined apertures created precise fiducials for fine alignment of the image sensor.
As part of this program, NOVO developed numerous fixtures for manufacturing and assembly, including all optical alignment hardware, custom high-resolution optical targets, and custom assembly hand tools. Pneumatically-clamped fixturing was developed for free-state machining of the investment-cast housing to preserve optical alignment surfaces through all stages of conventional machining. The investment-cast housing eliminated the need for internal brackets, reducing part count and overall assembly labor.
Summary
This development project spanned several years during which NOVO worked with key suppliers to develop the manufacturing processes for the critical components, produced functional prototypes, performed verification testing, and generated production documentation. A BOM cost reduction project was requested as follow-on work. NOVO was able to reduce the mechanical BOM cost by approximately 40% during this project.
Throughout the project, NOVO collaborated closely with the client’s in-house team. Our contributions resulted in three U.S. utility patents.